Technical information - Compabloc heat exchanger
Alfa Laval is the only supplier of bloc-type heat exchangers with more than eight decades of experience developing heat transfer technology. All of that expertise has gone into making Compabloc the unrivalled champion of heat exchange – with unique innovations that set it apart from the rest.
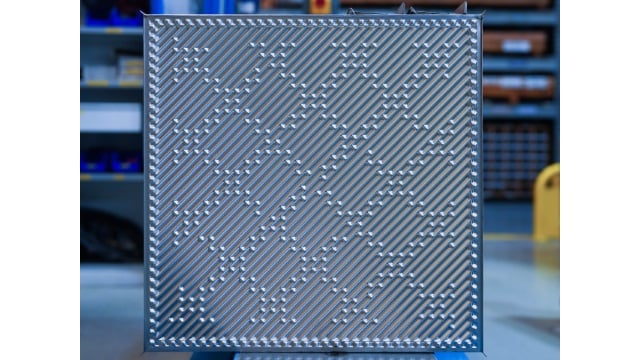
How does Compabloc work
Sitting at the core of every Compabloc is a stack of corrugated heat-transfer plates made of stainless steel or other corrosion-resistant materials, laser welded alternately to form channels.
The hot and the cold streams flow through alternate channels. Corrugated plates cause high turbulence, resulting in substantially higher heat transfer efficiency with a 50–80% smaller heat transfer area than comparable shell-and-tubes. Flow turbulence also reduces the build-up of fouling. The Compabloc’s unique plate design eliminates dead zones in the heat exchanger.
The two flows in a Compabloc can be configured as single pass, or as multiple pass by using baffles. The number of passes on the hot and cold side can be chosen independently, making it possible to optimize heat transfer even if flow rates on the different sides differ greatly. This unique flexibility means the Compabloc is always optimized for exactly the required duty. The baffles are made to withstand full vacuum, and can be rearranged if design conditions are changed in the future.
Compabloc units have a counter-current flow and can operate with a crossing temperature program (in a single unit), where the temperature approach is as close as 3°C (5.4°F), maximizing energy recovery. The small size and light weight makes it possible to install Compablocs anywhere, for instance at the top of distillation columns or suspended from support structures.

Compabloc - 1-pass condenser
Compabloc - 2-pass condenser
Compabloc liquid-to-liquid
Compabloc reboiler
Compabloc unique features
C-Weld™
Superior cleaning and extended performance
Alfa Laval manufactures the Compabloc plate pack using advanced laser welding with a butt-to-butt weld joint technique known as C-Weld. This eliminates crevices or “dead zones” common in other bloc-type heat exchangers, where fouling can build up, leading to corrosion and failure.
The use of laser welding and the C-Weld joint design further ensure higher reliability than conventional weld techniques, such as lap weld joints or TIG welding, which are far more susceptible to mechanical stress and failure. The end result is increased reliability and serviceability for maximum uptime.
SmartClean™
Fast and efficient flushing of fouling material
Alfa Laval’s C-Weld manufacturing method creates open channels around all the edges of plates in the Compabloc plate pack. During mechanical or chemical cleaning, as well as in the course of regular operation, any fouling that occurs will move along the heat transfer surface and flow freely out of these channels at the plate boundary. This SmartClean design makes it possible to fully clean every plate in the unit, returning the Compabloc to like-new performance after maintenance.
The SmartClean channels, impossible on bloc-type heat exchangers manufactured with edge welding, makes regular cleaning of the Compabloc both simple and quick.
+Seal
Confident, long-term performance under pressure
Unlike traditional flat gasket designs, +Seal introduces the first fully confined graphite gasket in a bloc-type heat exchanger. This prevents the risk of media leaks at pressures as high as 60 bar, simplifies maintenance, and protects against overtightening and creeping.
This is part of our revolutionary new Compabloc+ and is the secret to reaching higher design pressures without compromising on safety.
XCore™
Advanced design for higher pressures
Compabloc plates feature a one-of-a-kind pattern with “half-pyramids” equally distributed across the plate in an X-shaped pattern. This adds rigidity that increases mechanical strength for superior resistance to elongation forces common in high-pressure applications. With this cleanable XCore pattern, certain Compabloc models can handle pressures up to 42 barg without compromising thermal performance.
6 considerations for your selection process
Discover the plate heat exchanger benefits of Alfa Laval Compabloc
実証済みの信頼性
人々は一つの単純な理由でアルファ・ラバル Compablocs を選びます。 それらはまさしく作動しています。30,000 以上のユニットが配達されたことがその証拠です。 当社の実績ある製造および技術的なソリューションの結果、高い信頼性と長い耐用年数が得られます。 何十年もの間、連続して運転されてきた多くの Compabloc は、依然として最高のパフォーマンスを発揮しています。
持続可能性を改善するためのソリューション
Compabloc の高い熱効率の結果、Compabloc が熱回収に使用された場合、より高い熱回収、より低いボイラー燃料消費、およびより少ない CO2 排出量が得られます。
数か月で回収
高いエネルギー効率と低い設置および保守コストにより、Compablocs はシェル&チューブ式または他のタイプの溶接プレート式熱交換器などの他の技術よりもはるかに短い回収期間を提供します。 装置はしばしば数ヶ月で元がとれます。
生産量の増加と設置コストの削減
暖房や冷房に関連するボトルネックは、より効率的な熱交換器で解決できることがよくあります。 コンパクトサイズの Compabloc を使用すると、同じスペースにより多くの性能を詰め込むことができます。または、他の種類の機器のためにスペースを空けることができます。 それはまた設置費用がより低いことを意味します。
Ready for any duty
Compabloc is available in a wide range of sizes and is custom made to fit the specific operating and installation conditions. It can be made in virtually any material that can be pressed and welded.
Simplified maintenance for higher performance
Minimized fouling allows Compabloc to operate with cleaning intervals substantially longer than traditional heat exchangers, reducing lifetime maintenance costs. It is also the only welded heat exchanger where all channels, both hot and cold, can be fully cleaned using a hydro jet, bringing performance back to 100% after every cleaning.
HEXpert 熱交換器選定ツール
要求の厳しいプロセス向けに最適な熱交換器をすばやく見つけることができます。お客様の用途に関する情報を入力すると、5分以内にお客様のプロセスで熱交換器を活用する際の推奨事項を確認することができます。
