Plant-based drink production
Whether you are just getting started in plant-based drinks production, want to expand your production capacity, or diversify your product portfolio, we are here to help. With our state-of-the-art equipment, we can help optimize your production process, regardless of your capacity requirements or feedstock. Drawing on decades of experience from beverage processing, we help you enhance flavour, texture, and shelf life of your product, while minimizing investment and operational costs.
Start-ups
Are you looking to set up a new production plant for plant-based beverages? Our application experts can help you select the ideal processing equipment for a smooth scale-up from lab tests to commercial production.
Producers
If you are an existing plant-based beverage producer looking to expand, factors such as cleaning, uptime, operational and investment costs, and effective waste management significantly impact plant profitability. With the right equipment, Alfa Laval can help you uphold product quality and ensure high return on investment.
Dairies
Alternating between milk and plant-based beverages in your dairy can provide new revenue streams, but it also comes with new cleaning and waste handling requirements. We can help you upgrade your process line, and make sure your plant meets all regulatory demands.
From soy and oats to almonds, rice and beyond
Regardless of the raw materials you use, our team of specialists will help you choose the right solutions for your process based on your operating conditions and the unique characteristics of your feedstock and final product. We offer equipment for processing of soybeans, oats, almonds, rice, coconuts, cashew nuts, peanuts, walnuts and fruit pulp.
Typical plant-based drinks process
No two producers are the same, but the requirement for high-quality processing equipment is unanimous across the industry. Below you can see an example of a typical plant-based drinks process. Depending on the raw materials you have available, we can make a recommendation for a process solution tailored/suited for your particular plant-based drink production with focus on reliability, optimization of water and energy consumption and getting the most out of your raw material.
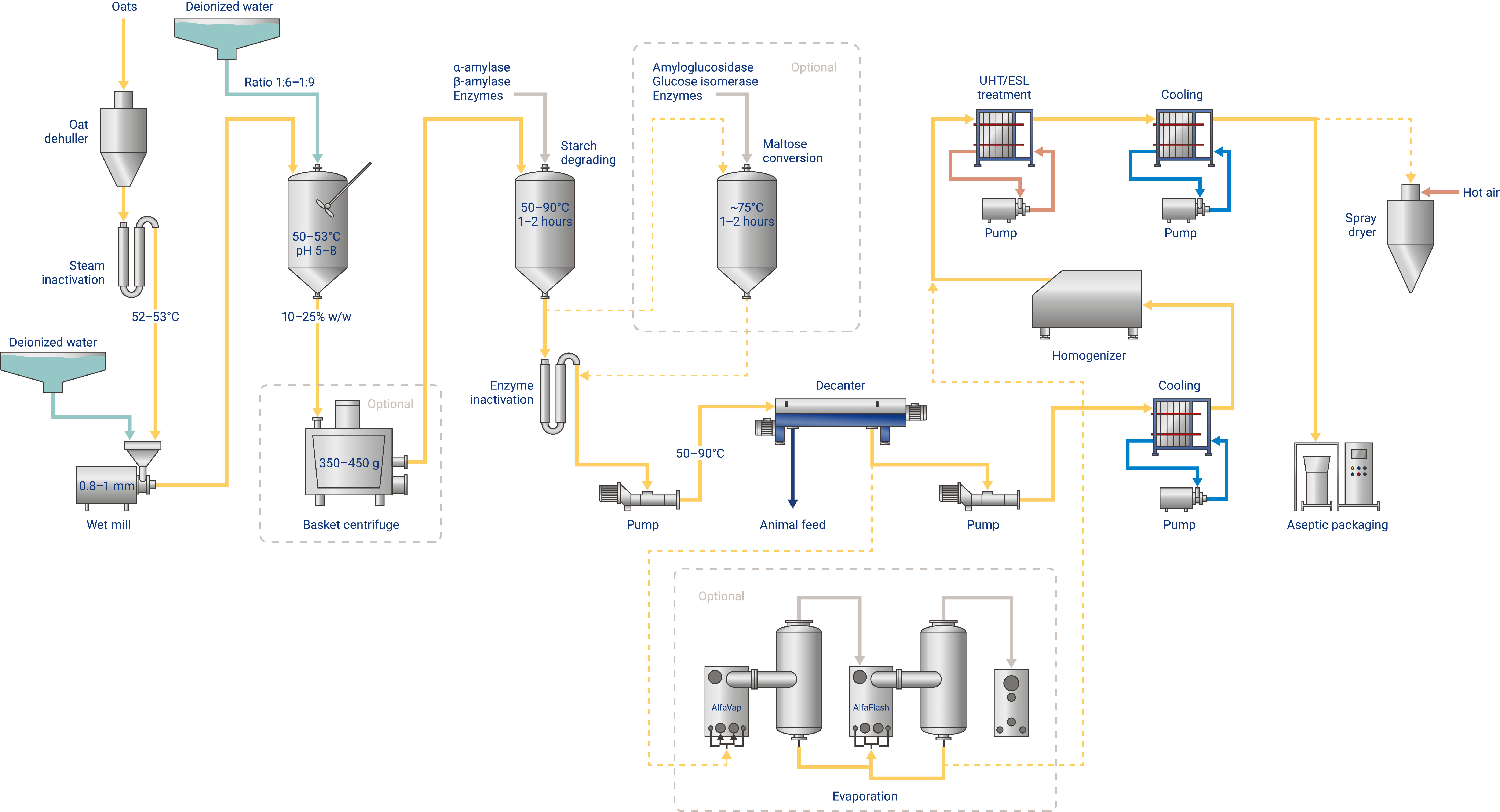
関連製品
Plantastic taste..
The equipment used in your plant-based drinks process has a profound effect on the taste and texture of your final products. Selecting the right heat exchangers, separation equipment, powder mixers, flow handling equipment, etc. is a prerequisite for high product quality and success in the market.
Avoid coagulation and burnt products
All heating and pasteurization steps risk affect taste negatively. If the product flow is too low and the temperature too high, proteins and sugars may cause a burnt taste in your product. We help you avoid these problems by supplying you with heat exchangers optimized for your operating conditions and raw material.
Create the perfect texture and taste
A perfect balance of solids and fats in your plant-based beverage is essential for great taste and texture, meaning separation stages are critical for product quality. We help you select the right separation equipment for your process, ensuring both high performance and sustainability.
Ensure hygiene and product safety
Spotless processing equipment is essential for both food safety and taste. Choosing inadequate equipment puts you at risk for cross-contamination between batches and residues of cleaning chemicals. The smooth surfaces and hygienic design of all Alfa Laval food processing equipment ensure it is easy to clean and that no residues remain after CIP.
… and a sustainability profile to match
A sustainable production process is a must for staying competitive in the plant-based drinks industry as more and more customers evaluate the environmental impact of the manufacturing process when choosing products. Click on the links below to learn how Alfa Laval products help minimize energy consumption, waste streams, CO2 emissions and water usage.
Energy savings
Our unique pump and valve solutions not only use minimal electrical power during operation, but also enable substantial reductions in hot-water consumption thanks to Alfa Laval's unique burst seat cleaning technology. Alfa Laval heat exchangers also offer up to 94% heat recovery when you recover and reuse energy from hot process streams to save steam.
Water savings
Environmental impact and water conservation has become integral in sustainable business strategies for companies, large and small. Using Alfa Laval Unique Mixproof valves and ThinkTop control units, you can save up to 90% of the water and chemicals used during cleaning.
Waste reduction
Together with your preferred integrator, we can supply complete, customized treatment plants for industrial wastewater, and help you reduce your waste to a minimum, recover valuable by-products, and even implement zero-liquid-discharge (ZLD) solutions.
Transportation savings
If you are an ingredients manufacturer producing base liquids, there are great savings to be made in transport-related emissions and costs if you concentrate your product before shipping. At Alfa Laval, we have extensive experience supplying systems based on evaporation or membrane technology. We can help you find the optimum solution based on your requirements and operating conditions.
導入時からのプロフェッショナルなサポート
食品、乳製品、飲料アプリケーション向けの設備サービスの経験を活かし、問題が発生した際や乳製品飲料生産のアップグレードの相談をしたい際に、いつでもサポートいたします。CIPプログラムの最適化に特化しており、水の消費と洗浄剤の使用を削減します。グローバルネットワークのパートナー、フィールドサービスエンジニア、サービスセンター、スペアパーツ流通ハブのおかげで、常に質の高いサポートと正規のスペアパーツを提供できます。
初期の設置と試運転の段階から、設備のライフサイクル全体を通じて、予防保守、アップグレード、リモートモニタリング、予知保全、トラブルシューティングなどでサポートします。
最大の稼働時間、パフォーマンス、投資利益率を確保します。提供するサービスについて詳しくはこちらをご覧ください:
デカンタ遠心機サービス サニタリー ポンプサービス 熱交換器サービス
技術ハイライト
Perfecting the taste of plant-based drinks
With Alfa Laval PondCtrl™, you can easily adjust the separation in your decanter, making it possible to finetune the taste and mouthfeel of your plant-based beverage, all while the decanter is operating. Alfa Laval PondCtrl™ is an automated system for controlling the liquid level, the pond depth, in your decanter centrifuge.
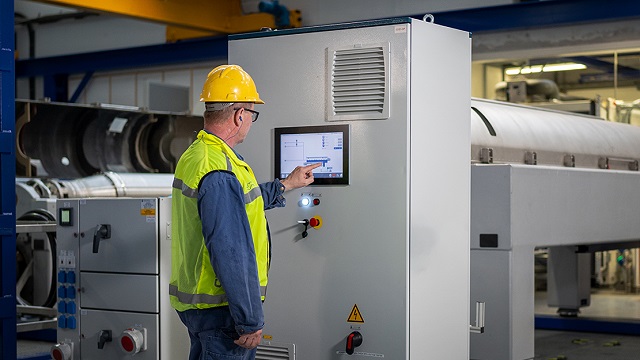
Customer stories
UK dairy uses Alfa Laval MBR membranes for their waste stream
"Operating costs have vastly reduced since the plant was installed and the MBR filters have been a pleasure to operate, with little involvement from any operators.” Alun Lewis – Head of Conformance & Sustainability.
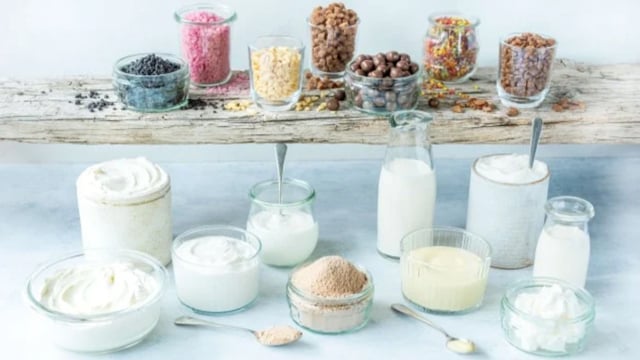
Photo courtesy of Meadow Foods